🔍研究
研究团队揭示了3D多孔超表面蒸发器的创新设计范式。前期,该团队曾通过烧结金属粉末构建了具有微尺度毛细网络的3D超表面蒸发芯体,实现蒸发效率的阶跃式提升。本次研究则是通过微纳3D打印技术再次构建了3D超表面蒸发芯体,并成功控制了孔隙间距的公差,为太阳能驱动蒸汽发生、工业余热回收等领域提供了创新性解决方案。
🌟亮点
基于之前的研究,研究团队设计的蒸发芯体采用晶胞基元结构,在单层多孔基底上集成毛细动脉网络,形成兼具液体输运与热扩散的双重功能体系。该结构通过延伸蒸发界面与持续基底润湿的协同作用,即使在300 kW/m²级高热流密度工况下仍能避免干涸现象。多尺度架构设计使毛细力-粘性力动态平衡达到最优,蒸发速率提升达50%,热效率逼近理论极限值(η=0.98)。而在本次研究实验中的六角形棱镜单胞蒸发器芯则是采用微纳3D打印技术制造而成。该芯厚度为375 μm,单元胞的孔隙率ε≈ 0.70,最大毛细管压力约为400 Pa。
研究团队在前期实验阶段采用石墨模具分层铜烧结工艺制备出具有毛细网络系统。然而,传统烧结工艺虽能实现结构成型,却受限于模具约束与材料单一性。相比之下,微纳3D打印技术通过无模具成型与多材料兼容特性,可灵活制备氧化铝、氧化锆等高性能陶瓷及特种聚合物芯体结构,突破模具法在结构自由度与设计迭代效率上的双重瓶颈。
📚来源
DOI:10.1016/j.ijheatmasstransfer.2025.127041
标题:3D-printed, ceramic porous metasurface wick: Hexagonal-prism unit-cell capillary evaporator
科研 微纳3D打印 3D打印 超表面 蒸发器 热效率 黑科技 陶瓷材料 科研狗
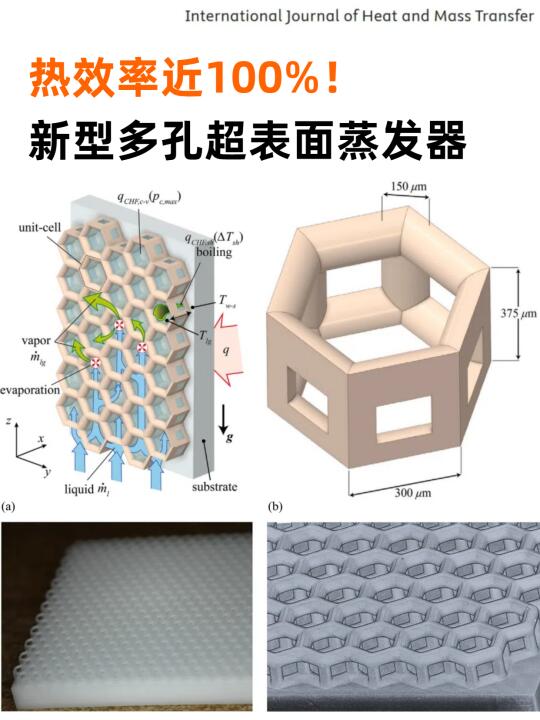
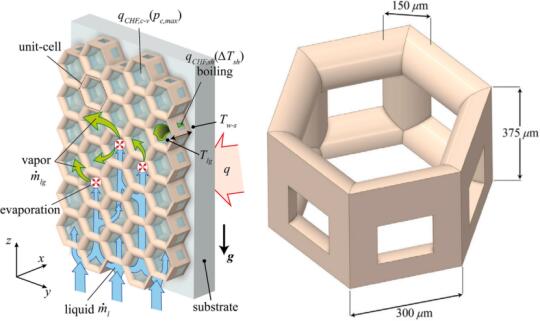
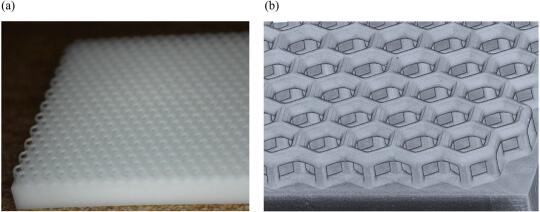
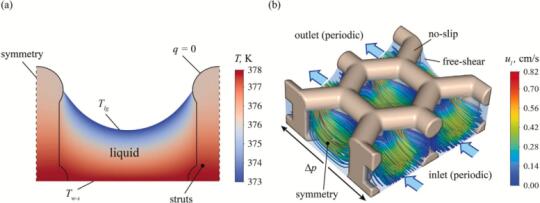
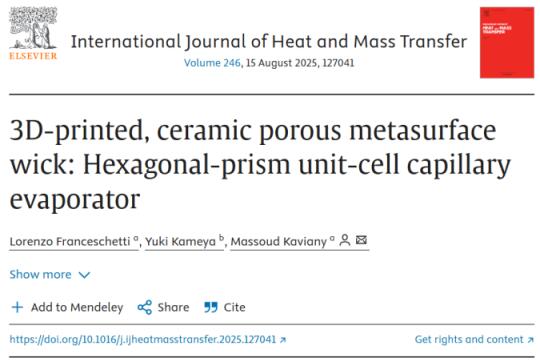